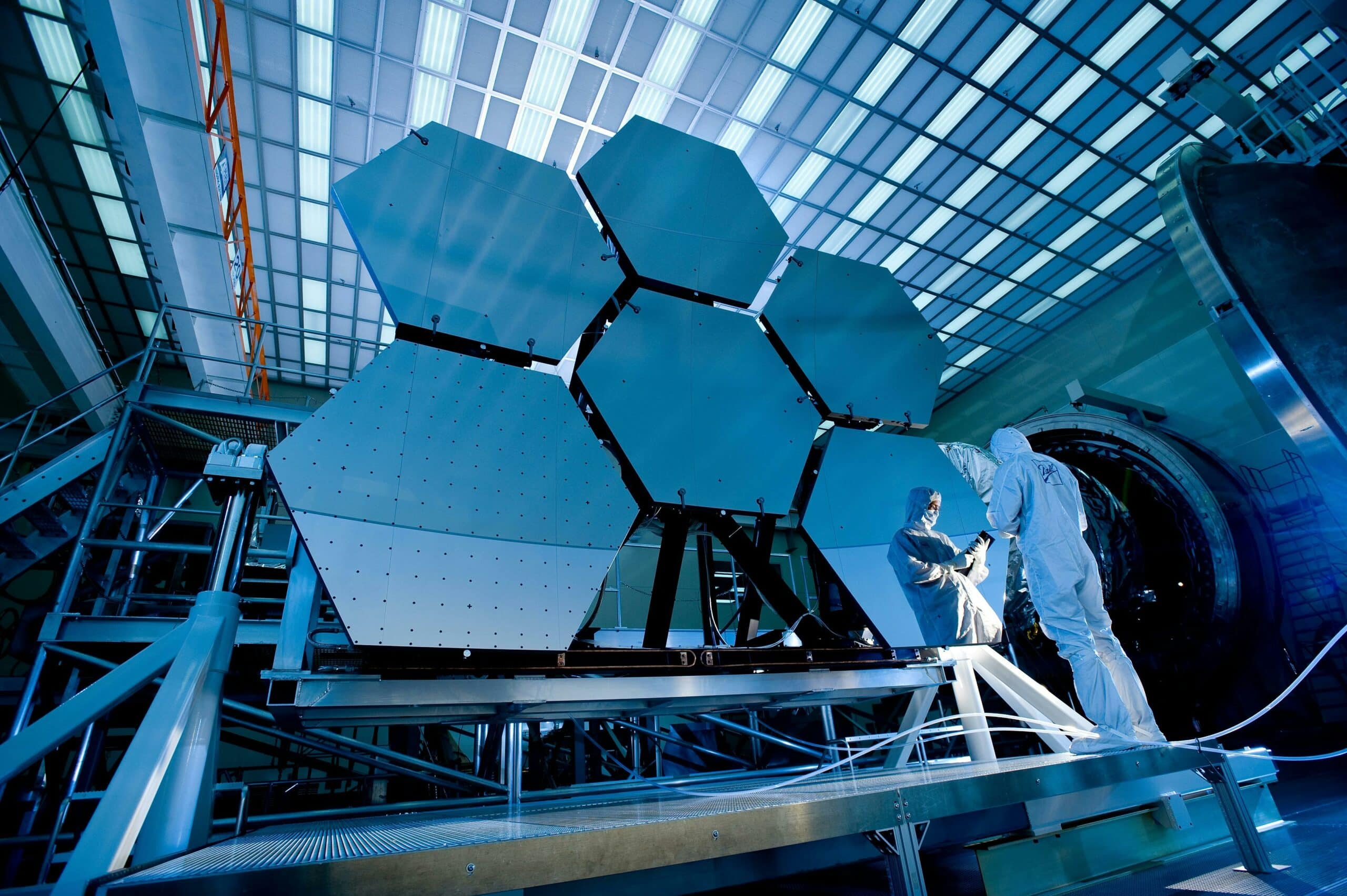
Les 10 innovations technologiques qui révolutionnent l’industrie 4.0
Partager l'article
Sommaire
Partager l'article
10 nouvelles technologies au cœur de l'industrie 4.0
L’évolution technologique redéfinit en profondeur le secteur industriel, alliant automatisation, interconnexion et intelligence des données. Grâce à ces avancées, les usines et entrepôts deviennent plus efficaces, flexibles et précis dans leurs processus.
Cet article met en lumière 10 innovations majeures qui révolutionnent la sécurité, la production, la logistique et la gestion des ressources.
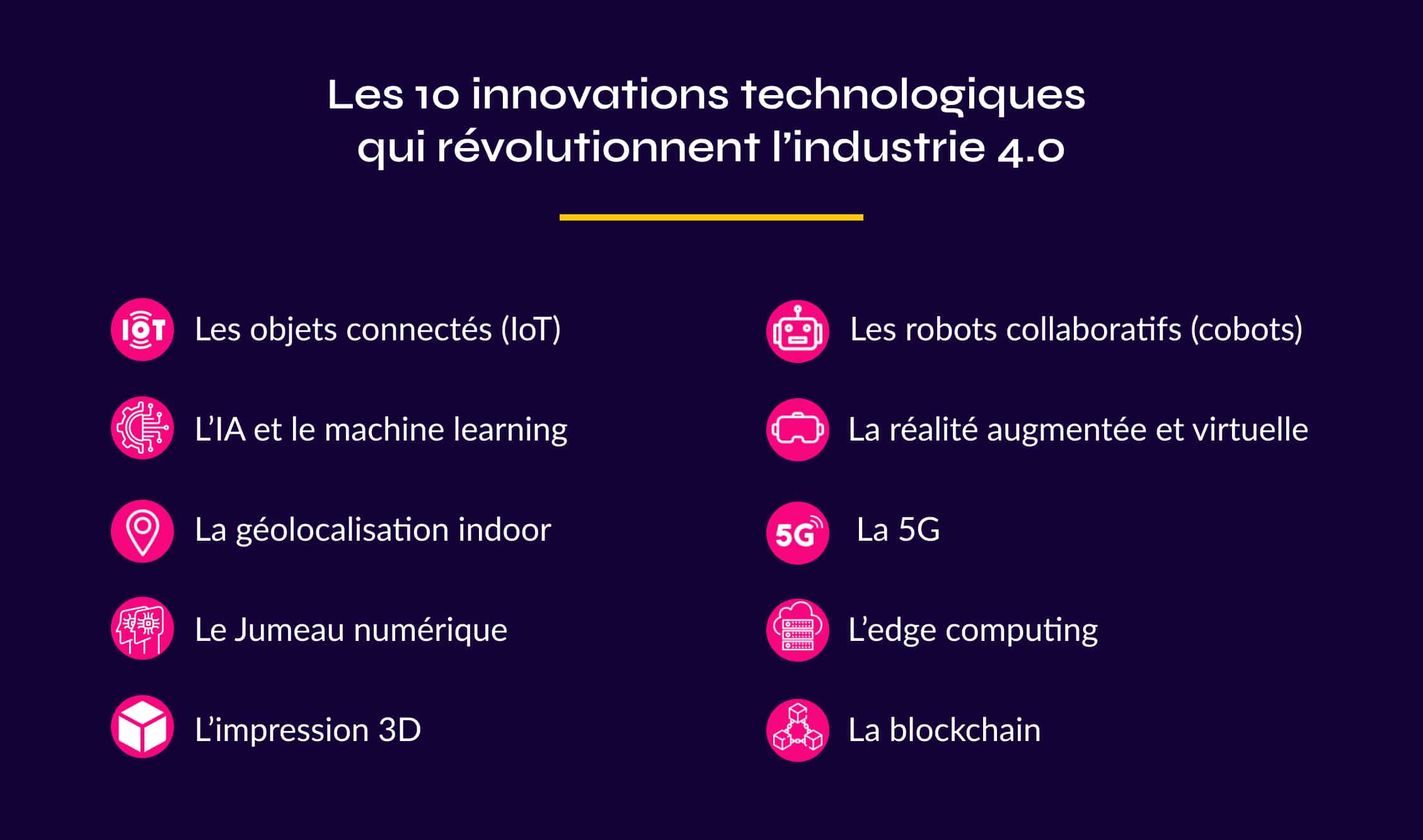
1. Les Objets Connectés (IoT) : connecter les machines pour une production optimisée
L’Internet industriel des Objets (IIoT) repose sur un réseau de capteurs intelligents connectés aux machines et aux infrastructures de production. Ces capteurs collectent, transmettent et analysent des données en temps réel, permettant ainsi un meilleur contrôle des processus industriels.
Grâce à l’IIoT, il devient possible de surveiller en continu l’état des équipements, de réduire les arrêts imprévus et d’optimiser la gestion des ressources. L’intégration de cette technologie contribue à une meilleure efficacité énergétique, une réduction des coûts opérationnels et une amélioration de la qualité des produits.
Cas d’usage
Surveillance en temps réel de la production et des performances des machines.
Maintenance préventive grâce à l’analyse des signaux envoyés par les capteurs.
Automatisation avancée des processus en fonction des données collectées.
2. L’intelligence artificielle et le machine learning : vers une industrie prédictive
L’intelligence artificielle (IA) et le machine learning permettent aux systèmes de détecter des tendances, d’anticiper les anomalies et de prendre des décisions autonomes en fonction des données traitées.
Elles jouent un rôle clé dans la maintenance prédictive, par l’analyse de l’historique des pannes et le comportement des machines pour prévenir les dysfonctionnements avant qu’ils ne surviennent. Elles sont également utilisées pour améliorer la gestion des stocks et l’optimisation des chaînes de production.
Cas d’usage
- Optimisation de la production en ajustant les paramètres en fonction des performances en temps réel.
- Détection d’anomalies pour prévenir les arrêts de production.
- Automatisation des contrôles qualité avec des algorithmes d’analyse d’images (computer vision).
La géolocalisation indoor repose sur des technologies comme le Bluetooth Low Energy (BLE), le Wi-Fi, le RFID ou l’Ultra Wideband (UWB) pour suivre précisément la position des équipements et des employés dans les usines ou les entrepôts. Contrairement aux systèmes GPS, inefficaces en intérieur, ces technologies permettent un suivi en temps réel des actifs industriels, améliorant ainsi l’optimisation des flux logistiques, la productivité et la sécurité des travailleurs.
Parmi les solutions existantes, Wheere se distingue comme la seule capable de traverser 50 mètres de béton. Sa technologie brevetée permet de couvrir un site industriel ou un complexe logistique avec seulement quatre antennes d’émission. Grâce à cette avancée, les entreprises peuvent localiser leurs actifs et leurs équipes avec une précision inférieure à 1 mètre, même dans des environnements où les autres technologies atteignent leurs limites.
Cas d’usage
- Optimisation des flux logistiques en identifiant l’emplacement des marchandises en temps réel.
- Protection du travailleur isolé PTI en réduisant le temps d’intervention en cas d’accident grace à la localisation précise des équipes.
- Asset tracking pour la réduction des pertes et vols de matériel.
4. Le Jumeau Numérique (Digital Twin) : une réplique virtuelle pour une gestion optimisée
Le Jumeau Numérique, ou Digital Twin, est une réplique virtuelle d’un objet, d’un système ou d’un processus industriel. Grâce à des capteurs IoT et des modèles informatiques avancés, cette technologie permet de simuler, analyser et optimiser un équipement ou une chaîne de production en temps réel, sans intervenir physiquement sur l’installation.
Les jumeaux numériques sont particulièrement utilisés pour anticiper les pannes, tester des améliorations avant leur mise en œuvre et optimiser l’utilisation des ressources. Cette approche permet une réduction des coûts, une amélioration des performances et une réduction des risques opérationnels.
Cas d’usage
- Optimisation des lignes de production en simulant différents scénarios avant leur application réelle.
- Réduction des temps d’arrêt en testant les ajustements techniques sans impacter la production.
- Formation des opérateurs dans un environnement simulé sans risques pour les équipements réels.
5. L'impression 3D : une production agile et optimisée
La fabrication additive, également connue sous le nom d’impression 3D, révolutionne les méthodes de production traditionnelles en permettant la création d’objets par ajout de matière couche par couche à partir de fichiers numériques. Contrairement aux procédés soustractifs tels que l’usinage ou le moulage, cette approche réduit considérablement les déchets et offre une liberté de conception accrue, facilitant la réalisation de géométries complexes et la personnalisation des produits pour répondre aux besoins spécifiques des clients.
Elle offre une grande flexibilité, en permettant la production de pièces personnalisées sans nécessiter d’outillage coûteux. De plus, elle accélère considérablement le développement de prototypes et la fabrication de composants complexes, ouvrant la voie à des designs innovants impossibles à réaliser avec des méthodes traditionnelles.
Cas d’usage
- Production personnalisée sans outillage coûteux.
- Réduction du temps de développement de nouveaux produits.
6. Les robots collaboratifs (cobots) : une automatisation flexible
Les cobots, ou robots collaboratifs, sont conçus pour travailler aux côtés des humains, contrairement aux robots industriels traditionnels qui opèrent en autonomie dans des zones confinées. Grâce à des capteurs avancés et des systèmes de vision intelligents, ils interagissent en toute sécurité avec les opérateurs tout en optimisant les tâches répétitives ou pénibles.
Cette collaboration homme-machine améliore la précision des opérations, tout en réduisant la fatigue des employés et en optimisant la productivité. Les cobots sont particulièrement utiles dans les environnements de production variée, où la flexibilité est essentielle.
Cas d’usage
- Simplification du processus d’assemblage et de montage de précision.
- Réduction de la pénibilité liée aux tâches répétitives et physiquement exigeantes pour les opérateurs.
7. La réalité augmentée et virtuelle : des outils immersifs pour l’industrie 4.0
La réalité augmentée (AR) et la réalité virtuelle (VR) transforment le secteur industriel en offrant des solutions immersives pour la formation, la maintenance et l’assemblage de précision.
Avec la réalité augmentée, les techniciens peuvent superposer des informations digitales (schémas, instructions, données de capteurs) directement sur les équipements qu’ils manipulent, réduisant ainsi les erreurs et accélérant les interventions. Cette approche est particulièrement efficace pour la maintenance assistée, où un expert peut guider un opérateur à distance.
De son côté, la réalité virtuelle plonge les utilisateurs dans un environnement entièrement simulé, idéal pour la formation des techniciens et l’optimisation des processus. Grâce à cette technologie, il est possible de simuler des situations à risque, permettant aux opérateurs d’apprendre à gérer des pannes ou des incidents sans exposer l’entreprise à des arrêts de production coûteux.
Cas d’usage
- Formation immersive des techniciens sur des machines complexes avant intervention réelle.
- Maintenance assistée à distance avec superposition d’instructions.
- Assemblage de précision avec guidage en temps réel.
- Simulations de situations dangereuses pour améliorer la sécurité sans risques réels.
8. La 5G : une connectivité ultra-rapide au service de l’industrie
L’adoption de la 5G dans l’industrie permet une communication instantanée entre machines, capteurs et systèmes informatiques. Grâce à son faible temps de latence et sa bande passante élevée, elle facilite des applications avancées comme le contrôle à distance des équipements, la maintenance assistée et l’automatisation intelligente des processus industriels.
L’un des principaux avantages de la 5G réside dans sa capacité à gérer des communications critiques grâce à des fonctionnalités telles que le découpage de réseau (network slicing). Cette technique permet de créer plusieurs réseaux virtuels sur une infrastructure physique commune, chacun optimisé pour des applications spécifiques, garantissant ainsi la qualité de service et la sécurité de bout en bout.
De plus, la 5G facilite l’intégration de technologies telles que la réalité augmentée (AR) et la réalité virtuelle (VR) dans les environnements industriels. Elle permet également le déploiement de véhicules autonomes et de robots collaboratifs (cobots) dans les usines, optimisant les flux logistiques et la production.
Cas d’usage
- Véhicules autonomes en entrepôt pour optimiser la logistique interne.
- Interventions de maintenance en réalité augmentée grâce à une connexion ultra-rapide.
9. L’Edge Computing : un traitement des données en local pour plus de réactivité
L’Edge Computing révolutionne la gestion des données industrielles en traitant les informations directement à la source, c’est-à-dire au niveau des machines et capteurs, plutôt que de les envoyer vers un serveur ou un cloud distant. Cela permet une réduction de la latence, une meilleure réactivité des systèmes et une diminution de la bande passante nécessaire.
Dans les environnements industriels où la rapidité de décision est cruciale, comme les lignes de production automatisées ou la gestion des équipements critiques, l’Edge Computing permet d’optimiser les opérations en temps réel, garantissant ainsi une meilleure sécurité des systèmes et une meilleure résilience en cas de panne réseau.
Cas d’usage
- Amélioration de la cybersécurité en limitant le transfert de données sensibles vers des serveurs externes.
- Optimisation des performances des machines en ajustant les paramètres en temps réel.
10. La blockchain : traçabilité et sécurité renforcées dans l’industrie
Connue pour son rôle dans le secteur financier, la blockchain trouve aujourd’hui des applications majeures dans l’industrie. Cette technologie de stockage et de transmission d’informations sécurisée et infalsifiable renforçant l’intégrité et la traçabilité des données issues de l’Internet des Objets (IoT) industriel. En enregistrant de manière immuable les informations générées par les machines et capteurs, la blockchain garantit que ces données n’ont pas été altérées, répondant ainsi aux préoccupations croissantes concernant la fiabilité et la légitimité des informations collectées. Elle permet également d’améliorer la traçabilité des produits, de garantir l’authenticité des matériaux et de renforcer la confiance entre les partenaires industriels.
Dans les chaînes d’approvisionnement complexes, où les matériaux et composants transitent par de nombreux intermédiaires, la blockchain offre une visibilité totale sur l’origine et le parcours des marchandises. Elle contribue également à réduire les fraudes et la contrefaçon, tout en facilitant les audits de conformité.
Cas d’usage
- Renforcement de la fiabilité et traçabilité des données issues de l’Internet des Objets
- Suivi en temps réel des matériaux et composants tout au long de la chaîne logistique.
- Certification automatique des produits pour garantir leur conformité aux normes.
L’industrie 4.0 : un avenir façonné par l’innovation technologique
L’industrie 4.0 évolue à un rythme effréné grâce aux nouvelles technologies qui optimisent la production, la logistique et la gestion des ressources. De l’intelligence artificielle à la géolocalisation indoor, en passant par la réalité augmentée et le Jumeau Numérique, ces innovations offrent aux entreprises industrielles un levier de compétitivité majeur.
Sources et liens utiles
- Wikipedia – L’internet industriel des objets (IIoT)
- L’Usine Nouvelle – Les objets connectés au coeur de l’industrie 4.0
- BPI France – Comment l’IA va-t-elle transformer l’industrie
- Industrie 4.0- jumeau numérique
- BPI France – Fabrication additive (impression 3D) : quelles applications dans l’industrie de demain ?
- Techniques de l’ingénieur – Les cobots au service de tous les industriels
- JDN – Industrie 4.o : la réalité augmentée redéfinit déjà l(assistance à distance
- McKinsey – Smarter Factories: How 5G can jump-start Industry 4.0
- Industrie40.fr – Edge computing
- Lemonde informatique – Industrie 4.0 & IoT : assurer l’intégrité des données par la blockchain
Vous avez aimé ?
Partagez-le et découvrez d’autres articles qui pourraient également vous plaire !
- News
- Articles
- News